Sorun giderme yöntemleri. Sorun giderme programı
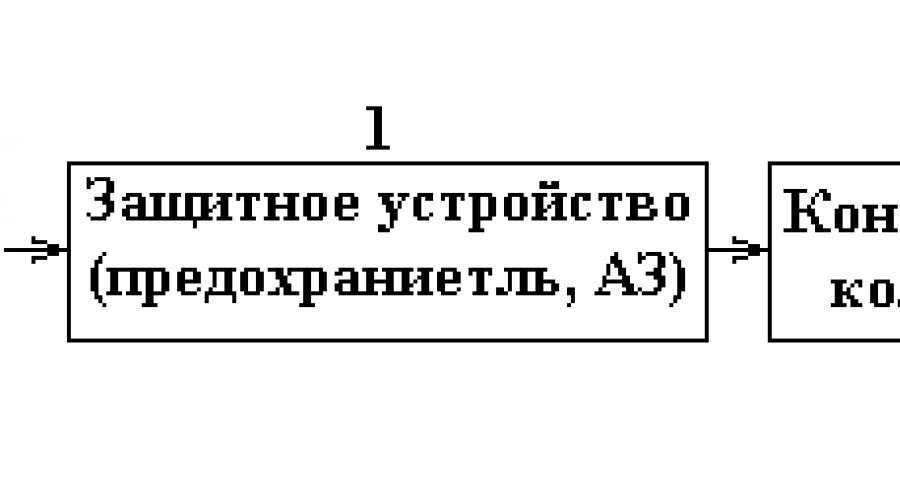
Arızalı bir elemanın bulunması onarım süresinin üçte birini alır. Otomasyon tesisleri nesnelerindeki öğelerin sayısı fazla olduğundan, durumlarını değerlendirmek için öğelerin doğrudan numaralandırılması imkansızdır. Sorun giderme çalışması yapılırken belirli kurallara uyulmalıdır. Arama teknolojisi, Şekil 3.1'de gösterilen temel işlemlere ayrılabilir.
Şekil 3.1 - Arıza arama teknolojisi (arızalar)
Sorun giderme süreci, çeşitli kontroller yapmaya ve kontrolün sonuçlarına göre aramanın daha da geliştirilmesine karar vermeye indirgenmiştir.
Sorun giderme sürecinin iki aşaması vardır: kontrol öğeleri dizisinin seçimi; bireysel doğrulama işlemlerini gerçekleştirmek için yöntemin seçimi.
Arama önceden yapılabilir belli sıra kontroller veya sonraki her kontrolün seyri bir öncekinin sonucuna göre belirlenir. Buna bağlı olarak aşağıdaki doğrulama yöntemleri:
- eleman eleman ardışık;
- ardışık grup;
kombinasyonel.
Kontrol sırasının seçimi, ürünlerin tasarımına bağlıdır ve kontrol elemanlarının güvenilirliği ve zahmetliliği hakkında bilgi toplama sürecinde değişebilir.
3.2.1 Sıralı eleman-eleman yöntemi sorun giderme sırasında ürünlerin öğelerinin belirli, önceden belirlenmiş bir sırayla tek tek kontrol edilmesinden oluşur. Bir sonraki kontrol edilen öğenin hizmet verilebilir olduğu ortaya çıktıysa, bir sonraki öğeyi kontrol etmeye devam edin. Arızalı bir eleman bulunduğunda arama durur ve eleman değiştirilir (onarılır). Ardından nesne çalışabilirlik açısından kontrol edilir. Aynı zamanda nesne (sistem) normal çalışmıyorsa, daha fazla doğrulamaya geçin. Ayrıca kontrol, hatalı elemanın tespit edildiği konumdan başlar. İkinci bir arızalı eleman bulunursa, o da değiştirilir veya onarılır (kurtarılır) ve nesne çalışabilirlik açısından yeniden kontrol edilir. Ve nesne veya sistem normal şekilde çalışana kadar böyle devam eder.
ÖRNEK Böyle bir yöntemin kullanımının en basit örneği, proses parametrelerinden birinin otomatik kontrol sisteminde sorun giderme olabilir. Önce regülatör, ardından aktüatör, ardından amplifikatör vb. kontrol edilir. Böylece, arızası otomatik kontrol sisteminin normal işleyişinde aksamaya neden olan bir nesne kurulur (Şekil 3.2).
Şekil 3.2 - Yapısal şema“Kristal” tipi otomatik kontrol sistemleri
Örneğin, aktüatörde bir arıza tespit edilirse, bu cihazın eleman-bazlı yapısı dikkate alınır (Şekil 3.3).
Şekil 3.3 - Aktüatörün yapısal diyagramı
Burada öğeleri kontrol etmek için aşağıdaki sırayı ayarlayabilirsiniz: 1-2-3-4-5-6-7-8. 1,2,4,7 ve 8 öğeleri en savunmasız olabilir.Bu nedenle, öğe bazında doğrulama yöntemini kullanırken, öğelerin kontrolünü sıralamanın iki yolu vardır.
Bir cihazda bir arıza ararken, öncelikle arızası cihazın normal işleyişinde bir aksamaya neden olan nesne tanımlanır. Ardından, arızalı cihaz nesnesinin eleman-eleman yapısı dikkate alınır.
Öğe bazında doğrulama yöntemini kullanırken, mümkündür eleman kontrol sırasının iki yolu.
1) Ürün, test süresi yaklaşık olarak aynı olan elemanları kullanıyorsa, test güvenilirliği en az olan elemanlarla başlamalıdır.
2) Belirli bir ürünün elemanlarının güvenilirliği yaklaşık olarak aynıysa, kontrol edilmesi en az zaman gerektiren elemanla kontrole başlanması tavsiye edilir.
Bu kuralların başarılı bir şekilde kullanılması için, nesnelerin ve sistemlerin yalnızca işlevsel ve şematik diyagramlarını bilmek değil, aynı zamanda öğelerinin güvenilirliği hakkında net bir fikre sahip olmak gerekir.
Yöntemin dezavantajı- nispeten çok sayıdaçekler. Bu, yöntemi evrensel kılsa da, bu yöntemin arama yaparken öğelerin işlevsel ilişkilerini kullanmaması gerçeğiyle açıklanmaktadır, çünkü sistemin işlevsel şemasına bağlı değildir.
3.2.2 Sıralı parti test yöntemi nesnenin tüm öğelerinin, işlevsel ilişkileri dikkate alınarak ayrı gruplara bölünmesi ve her grubun bir bütün olarak hizmet verebilirliğinin kontrol edilmesi gerçeğinden oluşur. Kontrollerin sırası bir önceki kontrolün sonucuna göre belirlenir. Kontroller yapıldıkça kontrol edilecek eleman sayısı azalır. Kontrolün son aşamasında grupta bir eleman bulunmalıdır.
Bu yöntemi kullanarak sorun giderme ÖRNEĞİ şu bölümde verilmiştir: fonksiyonel diyagramŞekil 3.4'teki sistem ACS türlerinden biridir.
Şekil 3.4 - ACS'nin blok diyagramına bir örnek
Şema I-VIII gruplarına ayrılmıştır. Daha sonra yapı iki alt gruba ayrılır ve bu böyle devam eder. Bu durumda, kontrollerin sırası aşağıdaki gibi olacaktır:
a) 4. noktadaki sinyal izlenir, eğer normalse 6. noktaya gidin, çünkü başarısız elemanın grup V, VI, VII, VIII'de olduğu varsayılır. 4. noktadaki sinyal norma uymuyorsa, 2. noktadaki sinyal kontrol edilir, çünkü I, II, III, IV öğelerinden biri arızalı. 2. noktadaki sinyal normal ise I,II elementleri sorunsuzdur ve 3.nokta kontrol edilmelidir.Bu, III veya IV elementlerinden hangisinin hatalı olduğunu gösterir.
b) 4. ve 6. noktaların kontrolü sırasında sinyal gerekli parametrelere karşılık geliyorsa, 5. nokta kontrol edilir ve bunun sonucunda hatalı bir eleman V veya VIII belirlenir.
Bu sorun giderme yöntemi ile test noktalarındaki sinyallerin parametrelerini bilmek gerekir.
Nesnede (sistemde) birkaç hata varsa, sorun giderme şeması değişmeyecektir. Yapının kollarından biri boyunca hareket edildiğinde, kaçınılmaz olarak hatalı elemanlardan birine gelinir. Bu arızanın ortadan kaldırılmasından sonra (elemanın restorasyonu), nesnenin çalışabilirliği kontrol edilir. Bir hata varsa, ikinci bir hatalı öğeye yol açması gereken arama süreci devam eder ve bu böyle devam eder.
Bu yönteme orta nokta yöntemi de denir. Ancak genel durumda bir nesnenin (sistemin) blok diyagramının bölündüğü sayı ikiye eşit olmayabilir. Bireysel elemanların işlevsel bağlantılarını ve işlerinin güvenilirliğini dikkate alarak sistemi parçalamak gerekir.
Grup çek yöntemi ile çekler ayırt edilir” bir istisna dışında" Ve " istisnasız”.
"Bir istisna dışında" kontrol, öğe gruplarından birinin çalışabilirliği hakkındaki sonucun, diğer grupların kontrolü temelinde yapılması gerçeğinden oluşur. Örneğin, üç element grubumuz var. Kontrol sonuçlarına göre 1. ve 2. grubun hizmet verebilirliği belirlendi, kontroller yapmadan hatalı elemanın 3. grupta olduğu sonucuna vardık.
“İstisnasız” kontrollerde tüm grupların performansı izlenir. Son aşamada, hata olasılığını ortadan kaldıran bir “istisna yok” kontrolü her zaman gerçekleştirilir.
İtibar test dizileri - sorun giderme süresinde önemli bir azalma.
Bu yöntem, bireysel öğelerin işlevsel ilişkileri ve bunların güvenilirliği hakkında bilgi gerektirir.
3.2.3 Öz kombinasyon yöntemi kontroller, birkaç parametrenin eşzamanlı ölçümünden oluşur. Tüm parametrelerin ölçüm sonuçlarına dayanarak, hatalı bir eleman hakkında bir sonuca varılır.
Bu yöntemi kullanmanın rahatlığı için, kontrol edilen parametrelerin durum tabloları derlenir. Bu durumda, öğe olarak bir blok, bir düğüm, sıralı dallanmamış bir basamak grubu seçmelisiniz.
Tablonun ilk dikey sütununda, blok diyagramın öğelerini ve ilk satırda - parametrelerini belirtin. Tablo aşağıdaki kurallara göre oklarla doldurulur.
Alternatif olarak, bir arıza yalnızca verilen eleman. Bu hata ilgili parametrelerin tolerans dışına çıkmasına neden olur. Tabloda bu parametrelerin karşısına "0" konulur. Belirtilen hata herhangi bir parametreyi etkilemiyorsa, bu parametreye karşı "1" ayarlanır.
ÖRNEK Blok diyagramda (Şekil 3.5), A, B, C, D parametrelerini ölçüyoruz.
1. öğenin hatalı olduğuna inanıyoruz. O zaman A, B, C ve D parametrelerinin tamamının toleransların dışına çıkacağı açıktır. Tablo 3.2'deki bu parametrelere karşı “0” ayarlanır, yani. tablonun ilk satırı yalnızca sıfırlardan oluşacaktır. O zaman 2. elementin arızalı olduğunu, A, B ve C parametrelerinin standartlara uymayacağını ve D parametresinin normal olacağını varsayarız. İkinci satıra "0001" yazılmalıdır. Böylece, tüm öğeler üzerinde yineleme yapın ve parametrelerin durumunu analiz edin. Aynı satırlar (Tablo 3.2'deki 7 ve 8), bu sistemin 7 ve 8 numaralı elemanların arıza parametreleri arasında ayrım yapmadığını gösterir. Bu durumda, elemanlar birleştirilir veya girilir. ek parametre onları ayırt etmek için
Şekil 3.5 - Kombine kontrol yönteminin kullanımına.
Tablo 3.2 - Durum Grafiği
Elementler | Seçenekler | |||
A | İÇİNDE | İLE | D | |
Böyle bir tablo kullanarak hatalı bir elemanı tespit etmek için aşağıdakileri yapın. Operatör parametre değerlerini belirtilen kurala göre sıfır ve birden oluşan bir sayı olarak yazar. Arızalı elemanın tespiti için ortaya çıkan sayı tablonun satırlarındaki sayılarla karşılaştırılır. Tablonun hangi satırı ölçüm parametrelerinin sonuçlarıyla eşleşiyorsa, o eleman hatalıdır. Parametre ölçüm sonucu (sayı) tablonun herhangi bir satırıyla eşleşmiyorsa, birkaç öğe hatalıdır.
İtibar Bu yöntemin nispeten kısa bir sorun giderme süresi vardır, ancak uygulanması zordur.
3.2.4 Sorun giderme işleminin sırası denir arama programları. Kontrol zamanının matematiksel beklentisinin minimum değerini sağlayan belirli bir kontrol dizisi, başarısız bir öğeyi arama sürecinin matematiksel bir modeli oluşturularak hesaplanır.
Arızanın meydana geldiği nesne şunlardan oluşur: N elementler. Eleman arızaları bağımsızdır. Öğelerden herhangi biri başarısız olursa, nesne başarısız olur. Elemanın sağlığını kontrol etmek için girişe bir kontrol sinyali uygulamak ve çıkışta bu sinyale verilen yanıtı kontrol etmek mümkündür. Eleman arıza oranları biliniyor Q ve gerekli süre τ doğruluğunu kontrol etmek için. En kısa sorun giderme süresini sağlayan öğelerin kontrol sırasını belirleyin.
Optimal dizi aşağıdaki özelliğe sahip olmalıdır
, (3.1)
burada τ, iyi bir öğeyi kontrol etmek için ortalama süredir;
q, eleman arızasının koşullu olasılığıdır.
Tüm öğelerin sağlık kontrolü süresi eşitse, optimal sıra şu şekli alır:
q 1 >q 2 >…>q n -1. (3.2)
Onlar. eleman hizmet verebilirlik kontrolü, eleman arızalarının koşullu olasılığının azalan sırasına göre yapılmalıdır.
Sıra (3.2) daha uygun bir biçimde yazılabilir.
λ 1 >λ 2 >…> λ n-1, (3.3)
Program için ortalama sorun giderme süresi formülle hesaplanır
, (3.4)
nerede τ FROM. i, i'inci elemanın arızalanması durumunda ölçümler için harcanan süredir.
sırası gelince
burada τR, şemanın R noktasındaki ölçümler için harcanan zamandır;
r i, i'nci elemanın arızasını tespit etmek için programa göre yapılan ölçüm sayısıdır.
dikkate alarak (3.5)
, (3.6)
Programları oluşturma sırası örneklerde görülebilir.
Örnek 3.1
Şekil 3.6 - A ürününün yapısal diyagramı.
Şekil 3.6'da gösterilen bir şema vardır. Elemanların başarısızlık oranları: λ 1 =0.1 h -1 ; X2=0.2 h-1; X3=0.2 h-1; λ4=0.5 h-1 . Şema noktalarında ölçüm süresi: τ 1 =5 dk.; t2 = 8 dak.; t3 = 12 dak.; t 4 = 18 dak. A ürününün unsurlarından birinin arızalanması koşuluyla, bir sorun giderme programı için en uygun şemanın hazırlanması gerekir.
Koşullu başarısızlık olasılıkları belirlenir. Ardışık eleman-eleman kontrol yöntemi için koşullu arıza olasılıkları q, λ değerine karşılık gelir. O zaman q 1 = 0.1; q2=0.2; q3=0.2; q 4 \u003d 0,5. Özel tanımla: τ 1 /q 1 =50; t2/q2 =40; t3/q3 =60; t4/q4 =36;
(3.1)'e göre ilk ölçüm dördüncü (IV) elemanın çıkışında yapılmalıdır. eğer sinyal istenen tip eleman IV'ün çıkışında, daha sonra arama devam etmeli ve sonraki ölçümler ikinci (II) elemanın çıkışında yapılmalıdır, vb.
Sorun giderme sürecinin analitik bir temsili için, kural olarak, grafik gösterimi bir sorun giderme programı biçiminde kullanılır. Sembol eleman dikdörtgen şeklinde yapılır ve ölçüm, arkasında ölçümün yapıldığı elemanın numaraları ile içte daire şeklinde yapılır. Daha sonra sorun giderme programı, ölçüm sonucunu gösteren (istenen bir sinyal var mı yok mu - "evet" veya "hayır") ve hatalı elemanı gösteren dikdörtgenlerle biten iki çıkışlı dairelerden oluşan bir dallanma şemasıyla temsil edilecektir.
Örnek 3.1 için arama programı Şekil 3.7'de gösterilmiştir.
Şekil 3.7 - A ürünündeki sorun giderme programı
Program için ortalama sorun giderme süresi formül (3.6) ile hesaplanır. Daha sonra:
T PN \u003d q 1 (τ 4 + τ 2 + τ 1) + q 2 (τ 4 + τ 2) + q 3 (τ 4 + τ 2 + τ 1) + q 4 τ 4 \u003d 0,1 (18 + 8+ 5)+0,2(18+6)+0,2(18+8+5)+0,5*18=23,5 dk.
Örnek 3.2.
Şekil 3.8'de gösterilen bir şema vardır. Elemanların başarısızlık oranları: λ 1 =0.56*10 -4 h -1 ; λ 2 \u003d 0,48 * 10 -4 sa -1; λ 3 \u003d 0,26 * 10 -4 sa -1; λ 4 \u003d 0,2 * 10 -4 sa -1; λ 5 \u003d 0,32 * 10 -4 sa -1; λ 6 \u003d 0,18 * 10 -4 saat -1. Tüm noktalarda ölçüm süresi aynıdır ve 2 dakikadır. Öğelerden birinin başarısız olması koşuluyla, optimum bir sorun giderme programı oluşturmak gerekir.
Şekil 3.8 - B ürününün yapısal diyagramı
Sorun giderme süresini azaltmak için sıralı toplu test yöntemi kullanılır, örn. kontrol sinyaline verilen yanıtın ölçümü, şüpheli hatalı devreyi olasılığa (yoğunluğa) göre ikiye bölen devre noktasında yapılır.
Bu nedenle, koşullu arıza olasılığı, 0,5 katsayılı (değerin yarısı) yoğunluk değerine karşılık gelir.
Sonra koşullu hata olasılıkları: q 1 =0.28; q2=0.24; q3=0.13; q4=0.10; q5=0.16; q 6 \u003d 0,09.
Devre seri bağlı elemanlardan oluşur. İlk elemanın girişine uygulanan bir kontrol sinyali kullanabilirsiniz. Bu durumda, ikinci elemandan sonra ilk ölçüm yapılmalıdır, çünkü q 1 +; q 2 \u003d 0,52, olasılık açısından şemanın ikiye bölünmesine en yakın olanıdır. İkinci elemandan sonra istenilen sinyal yoksa birinci veya ikinci elemanın arızalı olduğu sonucuna varılır ve birinci elemandan sonra ölçüm yapılır. İkinci elemandan sonra istenen bir sinyal varsa, devrenin sağ tarafında bir arıza olduğu sonucuna varılır; bu, muhtemelen dördüncü elemandan sonraki ölçüm noktasında ikiye bölünür vb.
Bu devredeki sorun giderme programı Şekil 3.9'da gösterilmiştir.
![]() |
Şekil 3.9 - B ürünündeki sorun giderme programı.
Program için ortalama sorun giderme süresi:
T P.N. =0,28(2+2)+0,24(2+2)+0,13(2+2+2)+0,20(2+2+2)+0,16(2+2+2 )+0,9(2+2+2) =5.56 dk.
3.2.5 Sorun giderirken, bir nesne (sistem) için bir yöntem ve sorun giderme programı seçmeye ek olarak, tek tek öğelerin sağlığını kontrol etmek için bir metodoloji (yöntemler) seçmek gerekir. en yaygın elemanların sağlığını kontrol etmenin yolları:
Görsel inceleme;
Kontrol anahtarları ve ayarlamalar;
Ara ölçümler;
Karşılaştırmak;
Tipik arızalar;
Bir bloğun veya kaskadın izolasyonu, düğüm;
Test - sinyaller.
Görsel inceleme genellikle görme ve işitme kullanımını içerir. SA'nın kurulum durumunu, kabloları, bireysel elemanları kontrol etmenize izin verirler. baskılı devre kartı vb. yanı sıra birkaç birimin çalışmasını daha az sıklıkla kulakla kontrol edin.
avantaj bu tür basitliği kontrol eder.
kusur– Arızalı elemanı belirleme olanakları sınırlıdır. Bir arıza ancak açıkça ifade edilen dış işaretlerle belirlenebilir: sıcaklığın etkisi altında elemanın renginde bir değişiklik, kıvılcım, duman görünümü ve yanan tel yalıtımından kaynaklanan koku vb. Bu tür belirtiler nadirdir. Ek olarak, pratikte birbirine bağlı arızalarla sıklıkla karşılaşılır, bu nedenle, harici bir inceleme ile hatalı bir eleman bulunsa bile, arızanın gerçek nedenlerini belirlemek için ek kontroller yapılmalıdır (örneğin, bir sigorta arızalandığında, yanmış iplik "gözle" görülebilir).
Kontrol anahtarlama ve ayarlama yöntemi devreleri analiz ederek ve anahtarlama, ayar, akım izleme elemanları (sinyal lambaları, yerleşik cihazlar, devre kesiciler, vb.) kullanarak harici arıza belirtilerinin değerlendirilmesini gerektirir. Bu durumda, nesne (sistem) şemasının hatalı bir düğümü, bloğu veya yolu belirlenir, yani. nesnenin belirli bir işlevini yerine getiren bir dizi öğe (dönüştürme, gösterge birimleri, koruma veya anahtarlama birimi, iletim yolu, vb.).
İtibar nesne devresinin bölümlerinin durumu hakkındaki varsayımı kontrol etmenin hızı ve basitliği yöntemi.
kusur– sınırlama, çünkü belirli bir hasar konumu yerine alanları tanımlamanıza olanak tanır.
Ara ölçüm yöntemi elektrik için en yaygın ve temel ve elektronik aletler. Bir sistemin, bloğun, düzeneğin veya elemanın parametreleri, elle taşınabilir veya otomatik yerleşik kontrol ve ölçüm cihazları (CIA) veya özel ölçüm cihazları, otomatik kontrol sistemleri kullanılarak belirlenir.
Aynı zamanda güç modları, iletişim hatlarının parametreleri ölçülür, kontrol noktalarında ölçümler yapılır. Arıza bulma hızı, büyük ölçüde bakım personelinin doğru ölçüm yapabilmesi ile sağlanır. Parametrelerin elde edilen değerleri, bu ürünün mod tabloları ile teknik dokümantasyondaki değerleriyle karşılaştırılır.
Değiştirme yöntemi arıza olduğundan şüphelenilen bir elemanın (montaj, blok vb.) yerine, iyi olduğu bilinen benzer bir elemanın takılması gerçeğinden oluşur. Değiştirildikten sonra, nesnenin (sistem) çalışıp çalışmadığı kontrol edilir. Aynı zamanda sistem parametreleri normal aralıkta ise, değiştirilen elemanın arızalı olduğu sonucuna varılır. Bu yöntemin avantajı basitliğidir. Ancak pratikte, bu yöntemin, ilk olarak, yedek elemanların olmaması ve ikinci olarak, yetersiz değiştirilebilirlik nedeniyle ayarlama ihtiyacı nedeniyle sınırlamaları vardır.
Bağımlı başarısızlıklar tekrar başarısızlıklarına yol açabilir kurulu eleman, bu nedenle, şüpheli öğe kolayca çıkarılabilir ve ucuz olduğunda bu tür bir test kullanılır.
karşılaştırma yöntemi - bir nesnenin veya sistemin hatalı bir bölümünün (düğüm, blok) modu, sağlıklı bir nesnenin benzer bir bölümünün modu ile karşılaştırılır. Yöntemin avantajı, mutlak değerler, ölçülen değerler ve parametreler hakkında bilgi sahibi olma ihtiyacının olmamasıdır. Aynı zamanda, bu yöntem oldukça karmaşık arızaların belirlenmesine izin verir. Bu yöntemin dezavantajı, yedek (tezgah) ekipman setine ihtiyaç duyulması ve sonuç olarak bu yöntemin yalnızca bir laboratuvarda kullanılma olasılığıdır.
-de karakteristik hatalar yöntemi ret, bilinen esasa göre aranır karakteristik özellikler. Bu tür arızalar ve belirtileri, SA'nın çalıştırma talimatlarında tablolar şeklinde sunulmaktadır.
Karakteristik hata tablolarının bir dizi dezavantajı vardır ve bunlardan en önemlileri şunlardır:
Tablolar, başarısızlık belirtileri ve arasında kesin bir ilişki sağlamaz. olası arızalar: birkaç farklı arıza, bir belirtiye bağlıdır ve genellikle görünümlerinin herhangi bir belirtisi yoktur;
Tablolar genellikle, arızaların nedenini açıklığa kavuşturmayı amaçlayan testler yapmak için talimatlar içermez. Tek bir dış işaret, arızanın belirli bir nedenini gösteremez ve onu bulmak için, kontrol cihazlarının göstergeleri ve test sonuçları dahil olmak üzere bir dizi dış işaretin mantıksal bir karşılaştırması gerekir;
Tablolar tarafından önerilen hata arama eylemleri, neden-sonuç ilişkileri içermez ve sıralarına göre dağıtılmaz, gerçek arama ise çeşitli kontrollerin (testlerin) açık bir dizisidir.
Test Sinyalleri çeşitli bilgisayarlarda, bilgi işlem cihazlarında yaygın olarak kullanılmaktadır. Bu test sırasında, kontrol edilen cihazın girişine belirli özelliklere sahip bir sinyal uygulanır. Çıkış sinyalinin analizi, arızalı elemanın yerini belirlemenizi sağlar.
Blok yalıtımı(düğüm, bölüm, kademeli) bazı durumlarda bir blok veya kaskadın, nesnenin diğer bölümleriyle çok sayıda işlevsel bağlantıyla bağlanması gerçeğiyle doğrulanır. Böyle bir ünite arızalanırsa, arızanın ünitenin kendisinde veya ürünün işlevsel olarak ilgili parçalarında nerede meydana geldiğini belirlemek zordur. Bazı işlevsel bağlantıların bağlantısını kesmek, bazen hatalı öğenin yerini belirlemenize olanak tanır.
Dikkate alınan özel sorun giderme yöntemlerinin her birinin önemli sınırlamaları vardır, bu nedenle enstrümantasyon ve otomatik ekipmanın onarımı uygulamasında genellikle birkaç özel yöntem birlikte kullanılır. Yöntemlerin bu kombinasyonu, genel arama süresini azaltır ve böylece başarısına katkıda bulunur.
Ekipmanda bir arıza aranırken çeşitli yöntem ve yöntemler kullanılmaktadır. Aşağıdaki sorun giderme yöntemleri vardır:
1. Sıralı eleman bazında kontroller.
2. Grup kontrolleri.
3. Kombinasyon.
Ardışık eleman-eleman kontrol yöntemi, sistemin elemanlarının önceden belirlenmiş belirli bir sırada birer birer kontrol edilmesinden oluşur.
Her bir elemanın test edilmesi sonucunda durumu belirlenir. Kontrol edilen öğe doğruysa, sırayla bir sonraki kontrol edilir. (Sinyal yolu boyunca sırayla veya önceden belirlenmiş başka bir sırayla kontrol edebilirsiniz). Tespit edilen hatalı eleman geri yüklenir, ardından ekipmanın kapsamlı bir kontrolü gerçekleştirilir.
Grup kontrollerinin yöntemi, bir veya daha fazla parametrenin ölçülmesiyle, arızaların olduğu bir grup elemanın belirlenmesidir. Ardından, hatalı olan da dahil olmak üzere bir öğe alt grubunu tanımlamayı mümkün kılan başka bir dizi ölçüm gerçekleştirilir.
Ardışık bir dizi kontrol sonucunda, hatalı parçanın alanı, belirli bir hatalı eleman takılana kadar kademeli olarak daraltılır.
Kombinasyon yöntemi, sorun giderme sürecinde belirli bir parametre setinin ölçülmesinden oluşur. Bu ölçümlerin sonuçlarına göre hatalı bir eleman belirlenir. Sistemin durumunun analizi, eksiksiz bir kontrol grubundan sonra gerçekleştirilir.
Herhangi bir sorun giderme yöntemini uygularken, ekipmanın (elemanlar, düzenekler, ekipman) durumunu kontrol etmek için birkaç yöntem kullanılabilir:
Dış denetim yöntemi, arızalanması beklenen blokların (montajların) incelenmesinden oluşur. Bu durumda esas dikkat elektrik tesisatının durumuna (izolasyon hasarı, kopmalar, kısa devreler, arıza izleri vb.) dış görünüş dirençler, kapasitörler, transformatörler, anahtarların kontak sistemleri, röleler vb.
Değiştirme yöntemi, sistemin hatalı olması gereken ayrı ayrı öğelerinin (bloklar, çıkarılabilir parçalar) açıkça çalışır durumda olanlarla değiştirilmesinden oluşur. Değiştirdikten sonra normal çalışma geri yüklenirse, değiştirilen elemanın arızası hakkında bir sonuca varılır.
Karşılaştırma yöntemi, teknik dokümantasyonda voltaj, direnç vb.
Kontrol anahtarlama ve kontrol yöntemi, ekipmanı art arda çeşitli çalışma modlarına geçirerek hatalı bir yolu veya birimi belirlemek için kontrollerin, ölçüm ve gösterge cihazlarının kullanılmasından oluşur.
Ara ölçüm yöntemi, diğer yöntemlerle kontrol edilemeyen düğümleri, blokları, ekipman öğelerini kontrol etmek için kullanılır.
Ekipmanın kontrol noktalarındaki durumu kontrol etmek için voltajlar, frekanslar ve diğer sinyal parametreleri ölçülür. Ölçüm sonuçları, teknik dokümantasyon verileriyle karşılaştırılır.
Yenilenmiş ürünler, ana ölçümlere uygunluk açısından test edilir. özellikler ve bunları (ayarlamalarla) TU tarafından belirlenen normlara getirmek.
Sorun Giderme Sırası
Onarıma devam etmeden önce, iyi çalışmak gerekir devre şeması ekipman, ön paneldeki kontroller ve performansı kontrol etmek için bir yöntem. Onarımda kullanılan cihazları da incelemek gerekir.
Tüm donanım arızaları üç gruba ayrılabilir:
1. Ekipman hiç çalışmıyor. Bu gibi durumlarda, gerçek bir arıza olasılığı ya güç kaynaklarında ya da ekipmanın ortak düğümlerinde yatmaktadır. Ekipmanın bir ve belki de basit bir nedenden dolayı çalışmaması mümkündür: bir sigorta yanmıştır, devrede bir açık veya kısa devre vardır, güç filtresinin elektrolitik kondansatörü kapanmıştır, vb. Bu "basit" sebep , ekipmanın uzun süre açık kalması, diğer parçaların arızalanmasına ve daha karmaşık arızalara neden olabilir. Bu tür bir arıza, tespit edilip ortadan kaldırılırsa ekipmanın normal şekilde çalışmaya başlaması ve ek ayarlamalar gerektirmemesi açısından basittir. Tek parçaların arızalanması nedeniyle ekipman her zaman çalışmaz. Arızalı bir parçanın değiştirilmesinin onu normal çalışmasına döndürmediği ve daha karmaşık ayarlamaların gerekli olduğu zamanlar vardır.
2. Ekipman tamamen işlevsel değil. Örneğin, yalnızca gönderme yolu veya alma yolu işlevseldir. Arıza, ilk durumda olduğu gibi, hatalı yolun tek tek parçalarının ve bileşenlerinin arızasıyla da ilişkilendirilebilir.
3. Ekipman çalışıyor, ancak teknik özelliklere uymuyor. Örneğin, sinyal bozulması, seviyelerin olduğundan fazla veya az tahmin edilmesi. Bu gibi durumlarda, transistör modunun değiştiği, radyo bileşenlerinin parametrelerinin değiştiği vb.
Bu nedenle, ekipmanın durumunu ciddi şekilde incelemek gerekir. Bu çalışma, transistörlerin güç modlarının ölçülmesinden, bir seviye diyagramının alınmasından vs. oluşabilir.
Ekipman açıldığında veya çalışma sırasında arızaların ortaya çıkması mümkündür. Herhangi bir nedenle (uzun süreli depolama, nakliye, düşük kalite) laboratuvarda onarımın temeli ilk seçenektir. önleyici çalışma vb.) birden fazla arıza meydana gelebilir. Her işyerinde bulunan ekipmanlar yapay olarak arızalara neden olmuştur. Arızaların nedenleri, kural olarak, dış muayene yöntemiyle belirlenmez. Bununla birlikte, genel olarak sorun giderme aşağıdaki sırayla gerçekleştirilmelidir:
1. Arıza belirtileri hakkında ilk bilgileri toplamak ve yanlış arızaları arayarak zaman kaybetmekten kaçınmak için harici bir inceleme yapın. Dış muayene sırasında gereklidir:
besleme geriliminin doğru verildiğinden ve güç anahtarlarının takılı olduğundan, bağlantı kablolarının güvenli bir şekilde bağlandığından, blokların paketlere sıkıca oturduğundan emin olun;
anahtarların, anahtarlama bloklarının doğru kurulumunu, sigortaların bütünlüğünü kontrol edin.
Ekipman açıldığında zaten arıza belirtileri ortaya çıktıysa, öncelikle alarm ve kontrol cihazlarının okumaları analiz edilmelidir. Bu durumda elde edilen bilgiler genellikle bir arızanın nerede aranacağını belirlemek için yeterlidir. Ekipmanın ses ve optik sinyalizasyon cihazları, aşağıdaki türler arızalar:
güç kaynaklarının ve yanmış sigortaların çıkışlarında voltaj kaybı;
uzak güç sisteminin arızaları;
doğrusal kontrol frekanslarının akım kaybı ve normal AGC çalışmasının bozulması;
üretim ekipmanının çıkışındaki taşıyıcı akımlarının ve kontrol salınımlarının kaybı.
Arızanın blok, düğümden önce zaten belirlenmiş olması durumunda harici denetim de zorunludur. Bu durumda harici inceleme, yanmış parçaları, kurulum arızasını, röle ve anahtar kontaklarını, lehimleme bütünlüğünü, dokunma eksikliğini, sabitleme güvenilirliğini, MRU motorunun çalışmasını vb. belirler.
Harici inceleme ile sorun giderme yöntemi, en çok acil durum niteliğindeki arızalar için etkilidir (duman, keskin koku, kontakların kıvılcımlanması).
2. Ekipmanın çalışabilirliğini kontrol ederek, yolların hatalı bölümlerini veya tek tek paketlerin veya blokların hatasını belirleyin.
3. Kontrol yuvalarındaki seviye diyagramını ölçerek, hasarlı bölge sağlık kontrolünde tanımlanmamışsa. Bu aşamada bazen değiştirme yönteminin kullanılması tavsiye edilir, örneğin bloğu yedek parça paketinden iyi bilinen bir blokla değiştirmek.
4. Arızalı üniteyi ekipmana tamir hortumları ile bağlayarak ve çeşitli noktalarda seviye ölçerek arızalı üniteyi belirleyiniz. Bu durumda, her zaman yüksek ölçüm doğruluğu için çaba gösterilmemelidir. Bir sinyalin varlığından veya yokluğundan emin olmak yeterlidir. Seviye diyagramını kaldırırken, ilk ölçüm noktası, ölçüm sinyalinin test edilen bölümün girişine doğru şekilde uygulandığından emin olabileceğiniz şekilde seçilmelidir. Sonraki her ölçümün noktası, kontrol edilecek alan içinde eşit derecede güvenilir iki parçaya bölünecek ve bağlantının mevcudiyetini sağlayacak şekilde seçilmelidir. ölçüm aletleri düğüm çıkışına. Bu yöntemle doğrulama için daha az zaman harcanır.
5. Düğümde hasar bulmak harici bir inceleme ile başlamalı, ardından çalışma modunda besleme voltajını kontrol etmeli, gerekirse tek tek elemanların servis verilebilirliğini kontrol etmelidir. Düğümün çalışma modları hakkında gerekli verilerin yokluğunda (çalışma belgelerinde, transistör elektrotlarındaki voltajlar tüm düğümler için gösterilmemiştir), iyi bilinen bir düğümün parametreleriyle karşılaştırma yönteminin kullanılması tavsiye edilir. veya değiştirme yöntemi.
6. Arızalı parçayı iyi bir parça ile değiştirin. Bundan sonra, onarım görmüş düğümde ve ardından blokta kontrol ölçümleri yapın. Bazı durumlarda (örneğin, amplifikatörleri, PKK'yı tamir ederken), tamir edilen birim, operasyonel belgelerdeki verilere tam olarak uyacak şekilde ayarlanır ve ince ayar yapılır.
Konu 1.18. Kurulum çalışması kablo ile. Kabloyu kurulum için hazırlama. Koşum örgüsü.
Plastik kılıflı ve polietilen izolasyonlu bir kablonun hazırlanması, kurşun kılıflı kabloların hazırlanmasından temel olarak farklı değildir. Her türlü kontrol (kılıfın sıkılığı, damarların kırılması ve ekranla iletişimi, ekranın kırılması, damarların yalıtım direnci için) kurşun kılıflı kablolarla aynı şekilde yapılır, ancak dikkate alınır. topraklama olarak çıplak bir bakır çekirdeğin kullanılması. Kılıfların ve damarların iyi durumda olduğundan emin olduktan sonra kablo konsollar üzerinde tel bandajlarla geçici olarak sağlamlaştırılır ve kesme işlemine geçilir.
Kablonun döşemeye hazırlanması, kablo ile tamburların yol boyunca arabalarda veya özel arabalarda taşınmasıyla başlar. Güzergah demiryolu hattının yakınından geçiyorsa, kablo hemen bir hendeğe döşendiği demiryolu platformlarında taşınır. Kabloyu toprağa döşemeden önce, kılıfının sıkılığını, damarların yalıtım direncini ve içlerinde kısa devre ve kopma olup olmadığını kontrol edin.
Tesisatı hazırlamak için öncelikle kablonun iki ucunun da kuyunun şekline göre (ekleme kuyuda yapılıyorsa) veya herhangi bir şekilde sabitlenmesi gerekir. Daha sonra kablonun her iki ucuna ısıyla büzülen tüpler takılmalı, bu tüpün çapı ise kablo çapından biraz daha büyük olmalıdır. Bir polietilen manşonun parçaları, ısıyla daralan tüplerin üzerine konur.
Ardından, kablonun ekran veri yolunu düzenlemek için tasarlanmış kablonun her iki ucuna özel kelepçeler takmanız gerekir. Kelepçeleri sabitledikten sonra polietilen kılıfı ve alüminyum bandı temizleyin. Sıyırma uzunluğu her iki kenarda 15 mm olmalıdır. Sonuç olarak eşit bir bağlantı elde etmek için bu uzunluk seçilmiştir. Kelepçeleri alüminyum bant üzerine takın ve kablonun ucuna sabitlemek için bir tornavida kullanın. Ardından, bir ekran veri yolu sağlamak için her iki kelepçeyi de geçici bir kabloyla bağlamanız gerekir. Şimdi kablo çiftlerini katmanlara ayırmanız ve çalmanız gerekiyor. Damarlardaki arızaları tespit etmek için çevirme gereklidir. Katmanlara ayırmak, gelecekte kablonun her iki bölümünü de hızlı ve en önemlisi doğru bir şekilde bükmeye yardımcı olur.
Kablonun "kırılma" ve "mesaj" olup olmadığını kontrol etmek için, kılıfın 150 ila 400 mm uzunluğundaki bölümleri uçlarından çıkarılır, bant yalıtımı kesilerek çekirdekten çıkarılır.
Demetleri ve katmanları sabitleyen ipliklerin ve bantların kesilmesi önerilmez. Kablonun bir ucunda 20 ila 25 mm uzunluğundaki kesitlerde tüm damarlardan izolasyon çıkarılır, ardından damarlar 10-50 çiftlik demetler halinde toplanır. Her bir demetin tüm çekirdekleri kısa devrelidir ve sıyrılmış kısımlarını çıplak bir bakır çekirdekle sıkıca sarar. Tüm demetler, sıyrılmış bir bakır çekirdeğin bir bölümü ile birbirine bağlanır. Kablonun ekranına veya metal kılıfına bir demet demet bağlanır.
Kablonun karşı ucunda bir açık test gerçekleştirilir. Ahizenin (veya kulaklığın) kabloları, pil ve kablonun ekranı (veya metal kılıfı) ile seri olarak bağlanmıştır. Tüpten serbest bir tel ile sırayla kablonun her bir damarına dokunun (Şekil 11.6). Dokunulduğunda tüpte bir klik sesi duyulursa, test edilen çekirdek çalışıyor demektir. Kırık bir çekirdeğe dokunduğunuzda tıklama olmayacaktır.
Test edilen iletkenler soyulmaz. Kablo bir demir testeresi veya sektör makası ile kesilirken, damarların uçlarının yalıtımın kenarının dışına çıkması nedeniyle temas sağlanır.
Hareket kolaylığı için, borudan çıkan serbest tel yan kesicilere bağlanır ve bunlar damarların uçlarına temas eder. Gerekirse, test edilen çekirdeğin yalıtımı sıyrılır veya ısırılır.
Cihazınızın montajını bitirdikten, son elemanı karta lehimledikten sonra, hemen açmak için acele etmeyin. Bir multimetre hazırlayın, devre şemasını ve devrenin tanımını açın.
Öncelikle doğru montajı kontrol etmeniz, kısa devre (kısa devre) olup olmadığını kontrol etmeniz gerekir. Tüm elemanların doğru şekilde lehimlendiğini düşünüyorsanız ve çevirdikten sonra kısa devre bulamadıysanız, izleri reçine kalıntılarından temizleyebilir ve güç uygulayabilirsiniz, ancak önce güç devresinin direncini kontrol etmelisiniz. şüpheli derecede büyük ve bu, topladığınız şemada belirtilmemişse, şemayı açmak için acele etmeyin, tekrar kontrol edin. Diyot köprüsünün doğru monte edilip edilmediği, güç devresindeki kondansatörlerin lehimlenmesi sırasında polaritenin gözlemlenip gözlemlenmediği vb. rölantide 2-3 amper yiyin. Güç devresine seri olarak birkaç ohm'luk düşük güçlü bir sabit direnç bağlayabilirsiniz, bu, cihazı arızadan kurtarabilir. Şema içeriyorsa güç transistörleri veya bir radyatör üzerine monte edilmiş mikro devreler, bunları birbirinden izole etmeyi unutmayın. Cihazları ilk kez açarken dikkatli olun, diyotlar ve elektrolitik kondansatörler yanlış açıldıklarında veya voltaj aşılırsa patlayabilirler. Ayrıca, kapasitörler genellikle hemen patlamazlar, ancak önce bir süre ısınırlar. Açık ve henüz yapılandırılmamış cihazları gözetimsiz bırakmayın.
sorun giderme
Sorun gidermeye başlamadan önce, tamir ettiğiniz cihaz size tanıdık gelmiyorsa, öncelikle bu cihaz, ne tür bir cihaz veya ne tür bir düğüm (PSU, amplifikatör veya başka bir cihaz) hakkında mümkün olduğunca fazla bilgi edinmeniz gerekir. , ve bu cihazın bir açıklamasını ve şemasını almanız gerekiyor. Kartı çıkarıp sökmeye başlamadan önce, kasanın içinde fazlalık, yırtık parça, kırık vb. bir şey olup olmadığına yakından bakın. .
Kartı seçmeye başlamadan önce, yüksek voltajlı seramik olanlar dahil tüm kapasitörleri boşaltın, yaklaşık 100 ohm'luk bir dirençle boşaltmanız gerekir. Bunu yapmayı unutursanız, kazara kısa devre olması durumunda veya hatta arama sırasında, lehimsiz radyo bileşenlerinde, sonuçlar korkunç olabilir, daha fazla eleman uçabilir ve siz de acı çekebilirsiniz. Bu çok önemli!
Kontrol her zaman güç ve voltaj kontrolü ile başlar, şebeke voltajını, sigortayı ve ardından güç kaynağını kontrol edin. Güç kaynağının çıkışındaki voltajı ve mümkünse çıkıştaki akımı kontrol edin. Voltaj normaldir ve bir ampul veya direnç bağlarsanız, voltaj keskin bir şekilde düşer veya hatta PSU korumaya girer. Gerilimin gereğinden düşük olduğu veya hiç olmadığı ortaya çıkarsa, diyot köprülerini, ardından voltaj regülatörünü - varsa, devredeyse transistörleri kontrol ederiz. Bazen en basit multimetre bile devrede bir arıza bulabilir. Kontrol ve sorun giderme her zaman cihazdan güç bağlantısı kesilerek yapılmalıdır! Tellere dikkat edin, çıplaklarsa kopmazlar. Kartlar birbirine vidalı kelepçelerle sabitlenmiş konektörler veya kablolarla bağlıysa, yeniden bağlamayı deneyin. Vidalı klemensler güvenilir değildir, temas zamanla kaybolabilir. Tahtayı tekrar açmayı deneyin, dikkatlice izleyin, ısınma için transistörleri, dirençleri hissedin.
Önümüzde lehimlenmiş radyo bileşenlerine sahip çıplak bir tahta var, bir büyüteç alıp radyo elemanlarının harici incelemesine başlıyoruz, yol boyunca koklayabilirsiniz ve bu bir şaka değil, yanmış radyo elemanı hemen hesaplanabilir. Böyle bir unsurun dış muayene ile tespit edilemediği görülür. Muayenede dirençlerin ve transistörlerin kararmasına dikkat edin, böyle bir eleman fark ederseniz hemen tahtadan lehimini çözün ve eleman çalışıyor olsa bile onu değiştirmek daha iyidir. Transistörler, başarısız olduktan sonra bile bir test cihazı tarafından çağrılır. Karttan lehimleyerek dirençleri ve diğer radyo bileşenlerini çağırmak gerekir.
Radyo bileşenlerini inceledikten sonra kartı ters çeviriyoruz ve yanmış ya da kısa devre var mı (örneğin radyo elemanlarının çıkışları uzunsa kapanabiliyor, bu yüzden dikkatli olun) ekipmanı yeniden monte ederken). Öğelere dokunun, direncin tahtada sendelediğini hissediyorsanız, muhtemelen ortadan kaybolmuştur. elektrik kontağı, lehimleyin. Tahtanın ince izleri varsa, kırılma ve mikro çatlaklar açısından kontrol edilmelidir.
Cihaz sizin tarafınızdan monte edilmişse, tüm radyo bileşenlerinin doğru şekilde lehimlenip lehimlenmediğini kontrol edin. Farklı transistörlerin farklı pin çıkışları vardır, diyotların da farklı tanımları olabilir. Her lehimlenmiş eleman için referans kitabını açın (eğer pin çıkışlarını hafızadan hatırlamıyorsanız) ve kontrol etmeye başlayın. Ne yazık ki, çoğu zaman bir radyo elemanı arızalandığında, elemanın kendisi servis edilebilir bir elemandan farklı görünmeyebilir. Hala bir devre arızası bulamadıysanız, tüm transistörleri ve elemanları lehimlemeniz ve çalmanız gerekecektir. Genel olarak, elemanları lehimlemeden devreleri kontrol edebilirsiniz, ancak bunun için en azından bir osiloskop ve iyi bir multimetreye ihtiyacınız var. Bu yazıda bir osiloskopla çalışmanın metodolojisine ve tekniğine girmeyeceğim. Devre basitse, hatalı elemanlar genellikle çok hızlı bir şekilde tespit edilir.
Mikro devreler genellikle bir başkasıyla değiştirilerek arıza olup olmadığı kontrol edilir, devreleri monte ederken mikro devrelerin altına özel paneller koymanızı tavsiye ederim, aniden çıkarmanız gerekirse bu çok uygundur. Ancak mikro devre soketsizse ve karta lehimlenmişse, mikro devreyi lehimlemeye başlamadan önce güç pinlerindeki voltajı kontrol etmenizi tavsiye ederim.
Mikrodenetleyici kullanılan devrelerde, açıldıktan sonra devre yaşam belirtisi göstermiyorsa, kurulum doğruysa ve radyo bileşenleri doğru şekilde lehimlenmişse, öncelikle onu yeniden başlatmayı denemeniz gerekir. Programlama sırasında bir hata oluşursa veya "sol" bellenim taşarsa, böyle bir MK devrede çalışmayacaktır.
Örneğin karttan bir direnç, diyot veya kondansatör lehimlemek istemiyorsanız (böylece raylar tekrar ısınmaz, aksi takdirde düşebilirler) ve sadece üzerinde günah işlerseniz, lehimlemeyi deneyebilirsiniz. buna paralel benzer bir unsur. Bunu kapasitörler, dirençler ve diyotlarla yapabilirsiniz, sadece iki direnci paralel yaparsanız, toplam direncinizin yarıya ineceğini unutmayın, bu nedenle yine de karttan bir direnç çıkışını lehimlemeniz gerekir, ancak kapasitörlerle, aksine, ne zaman paralel kapasitans artışı mesela devrede 220uF kondansatör varsa ona paralel 100uF lehimleyin cihazı kısa süreli açarsanız bundan bir şey çıkmaz. Kural olarak, dirençli kapasitörler çok nadiren arızalanır. Transistörlere gelince, lehimlenmeleri gerekir, hiçbir durumda aynısını koşullu olarak çalışmayan bir transistöre paralel olarak koymamalısınız.
Bobin veya minyatür transformatörlerin kullanıldığı devrelerde büyük miktar sonuçlar, ortadan bir dokunuşla bile, dönüşlerin başlangıcını ve sonunu gözlemlemeniz gerekir, eğer böyle bir devreyi başlattıktan sonra cihaz çalışmak istemiyorsa, çıkışları değiştirin.
Cihazınızın çalışmama sebebini bulduğunuzu ve kart üzerindeki bu elemanı değiştirdiğinizi düşünüyorsanız, enerji vermeden önce kartın lehim noktalarında kısa devre olup olmadığını kontrol ediniz. Tüm metal nesneleri, tornavidaları, rezistansları, tel parçalarını vb. bir kenara koyun. Allah korusun, güç kaynağı ve cihazı kontrol ederken kartın altında bir direnç yuvarlanacak ve kısa devre yapacak.
Görev
Şimdi küçük bir problemi çözmenizi öneriyorum, aşağıdaki şema yeterli basit blok güç kaynağı, özellikle bu diyagramda hatalar yaptım ve bazı öğeleri yanlış çizdim, tüm hataları bulmaya çalışın. Bunun kendi topladığınız cihazınız olduğunu, ancak açtıktan sonra çalışmadığını veya bazı öğelerin başarısız olduğunu hayal edin.
Çok dikkatli olun, burada çok fazla hata var, bunun gerçek bir cihaz olduğunu hayal edin, tüm hataları bulamazsanız, cihazı bir sonraki açışınızda bir şeyler tekrar başarısız olabilir.
Modern bilgi işlem teknolojisinde, özellikle çok bitli arayüz cihazlarında, gerekli geçişin olmadığı bir çizgi bulmak son derece zordur. elektrik sinyali. Dijital tasarımlarda genellikle kanal alıcı-vericilerinin elemanlarının veya aynı zamanda arabellek devrelerini kırdığı bilinmektedir.
Elektrik devrelerinde sorun giderme yönteminin açıklaması
Bu, incelenen elektrik devresinin gücünü açmadan dijital devrenin giriş / çıkış aşamalarında hızlı bir şekilde açık devre, kısa devre veya sızıntı oluşturmanıza olanak tanır ve bu da zahmetli " dijital sistemlerin bağlantılarının çalması".
Cihazın temeli bir eğri grafiğidir. Bununla, dijital bir sistemdeki hatalı bir alıcı/verici bileşenini osiloskop ekranında görsel olarak belirlemek kolaydır. ilkeli devre şeması cihaz Şekil l'de gösterilmektedir. 10.1.1.
Osiloskop ekranındaki geçerli sinyal türleri - şek. 10.1.2.
Radyo elemanlarının aranması bir karşılaştırma yöntemiyle başlar: 0-6 alıcı-vericilerinin girişlerinin / çıkışlarının veri bitlerinde bir görüntü konfigürasyonu olduğunu varsayalım ve veri biti 7'de farklı olabilir.
Bit 7 alıcı-vericisinde bir sızıntı olduğu varsayılmalıdır veya kısa devre, giriş/çıkış ile. İyi sonuçlar Bu taraftan AON'lerin G / Ç yapılarının bozuk radyo elemanlarının yerelleştirilmesi sırasında verilen, kişisel bilgisayarlar(ISA, VESA, PCI veri yolları, LPT arayüzleri olan özel kartlar). Bir transformatör T1 olarak, isteğe bağlı birleşik marka TN veya TAN kullanmak mümkündür.